The expert opinion of Huafeng radiator is announced.
Release time:
2024-06-26
The expert opinion of Huafeng radiator is announced.
Position |
Name |
Professional title |
Work unit |
Contact number |
Signature |
Remarks |
Team leader |
|
|
|
|
|
|
Group member |
Xu Bin |
Senior engineer |
Zhongkan Metallurgical Investingation Design & Research Institute Co.,Ltd |
13833068016 |
Xu Bin |
|
Wang Dehong |
Senior engineer |
Baoding Yida Environmental Engineering Technology Co., Ltd. |
13933228546 |
Wang Dehong |
|
|
Wang Shan |
Senior engineer |
Baoding City Monitoring Center |
17332172127 |
Wang Shan |
|
|
|
|
|
|
|
|
|
|
|
|
|
|
|
|
|
|
|
|
|
|
|
|
|
|
|
|
|
|
|
|
|
|
|
|
Year, month, day
Opinions on environmental protection acceptance after completion of the reconstruction project of sheet painting production line of radiator branch of Hebei Huafeng Industrial Group Co., Ltd.
On June 29, 2018, Hebei Huafeng Industrial Group Co., Ltd. conducted an acceptance of the completed environmental protection acceptance of the radiator branch of Hebei Huafeng Industrial Group Co., Ltd.'s scattered coating production line renovation project, in strict accordance with relevant national laws and regulations, in accordance with the monitoring report and the Interim Measures for Completion Environmental Protection Acceptance of Construction Projects. The technical specifications/guidelines for completion environmental protection acceptance of construction projects, the environmental impact assessment report of this project, and the approval decision of the approval department were strictly followed, and the following opinions were put forward:
I. Basic situation of engineering construction
(I)Construction location, scale and main construction contents
Construction location: the project construction site is located inside Hebei Huafeng Industrial Group Limited Company factory, in Songlindian Town, Zhuozhou City, Hebei Province. The central geographical coordinates of the project are 39 "25' 55.27" north latitude and 115 "56' 55.37 " east longitude. The east side of the plant is abandoned sand and gravel factory and farmland, the south side is farmland, the west side is Huafeng living area, and the north side is Zhuozhou Haoyuan Box Industry Co., Ltd., driving school and printing factory.
Nature of the project: technical renovation.
Production scale and product plan: the spray area is 290000 m2. Including annual production of radiator: 29000m2, cooler: 111sets, butterfly valve: 30000.
Construction content: the working procedure of hot oil flushing inner cavity is changed to drying after washing with water (electric heating); the transformation of waste gas treatment facilities supporting paint, surface spray paint, repaint, cooler and butterfly valve spray painting in radiator: eliminate the existing phosphating wastewater treatment facilities, build an integrated automatic sewage treatment facility with 8m2/d treatment capacity, build a new active hair desorption combustion device, and increase mobile welding smoke purifier in welding process.
(II)Construction process and approval of environmental protection
Hebei Huafeng Industrial Group Co., Ltd. commissioned Beijing North Energy Saving and Environmental Protection Co., Ltd. to complete the Environmental Impact Report on the Reconstruction Project of Sheet Painting Production Line of Radiator Branch of Hebei Huafeng Industrial Group Co., Ltd in March 2017. the approval of the project was obtained from Zhuozhou Environmental Protection Bureau on June 28th, 2017.the approval number is: Z. H. B. [2017] 05.
Construction of the project began in August 2017 and it began trial operation in February 2018. And the acceptance test was carried out from February 5 to 7, 2018. Since the establishment of the project, there have been no environmental complaints, violations or penalties.
(III)Investment situation
The total investment of the project is expected to be 7.8 million yuan, of which 1.48 million yuan is invested in environmental protection. The actual total investment of the project is 7.88 million yuan, of which the actual environmental protection investment is 2.19 million yuan, accounting for 27.8% of the total investment.
(IV)Acceptance range
This acceptance includes the construction and operation of environmental protection facilities and environmental management of the project.
II. Engineering changes
After on-site investigation and verification with the construction unit, the changes of the project are as follows:
1)The EIA estimates that the waste gas from the paint mixing room and the waste gas from the fixed painting room are treated by an activated carbon adsorption box, but in the actual construction, the waste gas from the painting room and the fixed painting room are treated by their respective activated carbon adsorption devices and then discharged by an exhaust tube.
2)The EIA predicts that the waste gas from the primer drying process and the waste gas from the primer and replenishment process will be discharged after entering a set of activated carbon adsorption facilities, the actual construction situation is that the waste gas from the primer drying process and the waste from the coating and mending process share a set of activated carbon adsorption device for discharge.
3)In the EIA, the phosphating process does not write about how to take pollution control measures for the waste gas produced by de-oiling, derusting and phosphating. In the actual construction, it has been adopted to collect all the waste gas from the phosphating process and then discharge it after being treated by the acid fog purification tower.
4)The heating mode adopted in the scheme of activated carbon desorption combustion equipment is natural gas heating. In the actual construction, the electric heating self-low temperature catalytic combustion scheme is adopted, which is more energy-saving and environmental protection.
5)The EIA estimates that the wastewater from the project will be pretreated to meet the third-level standard of Integrated Sewage Discharge Standard (GB8976-96) and then discharged to the sewage treatment plant of Songlindian Town for further treatment. The actual situation is that the wastewater of the project is pretreated and discharged to the sewage treatment station of Huafeng Group Co., Ltd., and further treated to meet the first-class A of the Drainage Standard of Urban Sewage Treatment Plant, and finally discharged to the North Jvma River. The change of drainage direction has been put on record, and the river water treatment station of Huafeng Group has passed the acceptance.
III. Construction of environmental protection facilities
(I)Waste water
The waste water discharged by the project mainly includes degreasing and rust removing washing wastewater and phosphating washing wastewater. The waste water from the painting process and the domestic sewage of the staff and workers. In the process of degreasing, derusting and phosphating, the water in the washing tank is discharged regularly and the water in the tank is recycled. The phosphating wastewater is pretreated by the new sewage treatment system in the workshop and discharged into the sewage treatment station of Huafeng Group Co., Ltd. The lacquer wastewater produced by the project spray painting process enters the pool of the spray painting workshop, adding coagulant (coagulant aid) to make the paint in the waste water coagulate and float, the condensate is removed regularly, and the water is recycled and replenished regularly, discharged into the factory catchment pool every 2-3 months. After being treated by sewage treatment facilities of radiator branch, other production wastewater and domestic sewage treated by septic tank are discharged into Jvma River after treatment by sewage treatment station of Huafeng Group Co., Ltd.
(II)Exhaust gas
①Exhaust gas from paint mixing room and fixed painting process
The paint used in the radiator workshop of the project is carried out in the paint mixing room, and the organic waste gas is produced in the paint mixing process, and the main pollution factors are non-methane total hydrocarbons and xylene. The paint mixing room has its own fan. After adsorption by activated carbon, it is discharged through a 15m exhaust tube.
The fixed spray room is used for spraying and drying special topcoats. Paint fog is produced in the painting process, and the main pollution factors are non-methane total hydrocarbons, xylene and particles. The paint fog in the painting process is absorbed by water curtain paint mist purifier and filter cotton, and then collected into a set of activated carbon adsorption device by two fans (one for each painting room). Collect into one set of activated carbon adsorption device. The treated exhaust gas and the treated exhaust gas in the paint mixing room are discharged by using one 15m exhaust pipe together
②Waste gas from inner cavity painting process
When the inner cavity paint is applied in the painting room, the main pollution factors are non-methane total hydrocarbons and xylene. The process adopts closed workshop and ground suction to collect organic waste gas. The collected waste gas is treated by cotton filter and activated carbon adsorption device and then discharged by 15m exhaust tube.
③Primer coating and repainting process
The primer coating and repaint are carried out in the bottom reading room of the radiator spraying workshop, the paint exhaust gas is treated by water spin paint fog treatment equipment and filter cotton, and the primer coating waste gas passes through filter cotton, and the two strands of gas are finally discharged into a 15m high exhaust cylinder after being treated by activated carbon adsorption device.
④Spray the top paint. Waste gas from repainting, drying and primer coating drying
The primer coating, repainting, and air drying processes are carried out in the topcoat workshop of the radiator spraying workshop, and the repainting waste gas is discharged from the spray surface after being treated by water spin paint fog treatment equipment and filter cotton. The air-drying waste gas and the primer drying waste gas are absorbed by the activated carbon adsorption device and then discharged through a 15m high exhaust pipe.
⑤Exhaust gas from cooler spraying workshop
The cooler spraying production line is divided into 2 sets of spray lines, which are respectively absorbed by water curtain paint mist purifier, filter cotton and activated carbon, and then discharged by a 15m high exhaust cylinder. The workshop is a telescopic paint spraying room, mainly for cooler spraying and drying, the cooler spray is all air dried. There is no drying room and facilities.
⑥Butterfly valve spraying production line
The butterfly valve workshop is equipped with a painting room and 2 drying rooms. After passing through a water curtain paint mist purifier and filter cotton device in the paint spraying room, as well as two drying room exhaust gases, they enter one set of activated carbon adsorption devices for treatment and are discharged through a 15m high exhaust pipe
⑦Activated carbon desorption of exhaust gas from combustion device
The organic waste gas desorbed by activated carbon is discharged through 15m exhaust pipe after "direct combustion + catalytic combustion". The burner is directly heated by electric heating.
⑧Phosphating process waste gas
The waste gas is produced in the heating process of phosphating process, which is collected by side suction system and treated by acid fog purification tower, and then discharged by 15m exhaust tube.
⑨Welding process exhaust gas
The noise source of the project is mainly the noise produced by all kinds of fans. Noise reduction measures such as noise elimination measures, soft connection of import and export, sound insulation of factory building, distance attenuation and so on are adopted.
(IV)Solid waste
After domestic waste collection, it is regularly sent to the designated place of the sanitation department for disposal. The waste activated carbon is stored as dangerous waste, desorbed in the plant and then returned to production, according to the waste activity of each process. It is replaced once a year and desorbed and transported as general waste to the designated place of the sanitation department for disposal. Waste paint buckets of water-based paint are regularly recycled by manufacturers. The paint residue, waste filter cotton, oily paint waste bucket, sewage treatment equipment sludge, and hazardous waste produced by the phosphating process of internal cleaning residue are all stored in the temporary storage room of hazardous waste in the plant area. It is regularly collected and disposed of by Cangzhou Jihuan Veolia Environmental Service Co., Ltd., which is qualified for hazardous waste disposal.
(V)Other environmental protection facilities
1.Environmental risk prevention
There is no water collection pool in the project. Rain water is directly discharged into the rain water pipe network and then flows into the Jvma River.
The enterprise has prepared an emergency plan and put it on record with the Environmental Protection Bureau, and the record number is 130681-2018-050-L.
2.On-line monitoring device
The waste water discharge outlet of river water station of Huafeng Group is equipped with flow meter, ammonia nitrogen on-line monitor and COD on-line monitor. A monitoring platform is installed at the exhaust outlet, and there is a monitoring hole in the exhaust pipe, which has passed the standardized acceptance of the exhaust outlet. There are standardized identification plates for waste water and waste gas discharge outlets.
IV. Debugging effect of environmental protection facilities
During the monitoring period, the production of the project was stable, and the production equipment and pollution control facilities operated normally. During the monitoring period, the average production load of radiator spraying workshop was 87.5%, and that of screw valve spraying workshop was 94%. The average production load of cooler spraying workshop is 78.6%, and the production load of activated carbon desorption process is 82.5%.
1.Waste water
During the monitoring period, the daily average concentration or range of the main pollutants in the phosphating water outlet of the project is: pH7.62~ 7.93, COD359mg/L, total zinc 1.44mg/L, total phosphorus 4.22mg/L; the daily average concentration or range of the main pollutants in the main outlet of the production area is: pH7.21~7.52, COD27mg/L, ss suspended matter 13.2mg/L, ammonia nitrogen 3.61mg/L, total zinc 0.86mg/L, total phosphorus 3.25mp/L. The discharge concentration can meet the third grade standard of Integrated Sewage Discharge Standard (GB8976-96) and the influent quality requirements of Hebei Huafeng Group sewage treatment Station at the same time.
The daily average concentration or range of the main pollutants at the discharge outlet of the sewage treatment station of Hebei Huafeng Group Company is: pH6.48-6.71,COD43mg/L, ammonia nitrogen 1.68mg/L, total ammonia 4.53mg/L: total phosphorus 0.38mg/L, total zinc 0.64mg/L, the discharge conforms to the first class A standard of Urban Sewage Treatment Plant Pollutant Discharge Standard (GB18918-2002).
2.Exhaust gas
During the monitoring period, the maximum concentration of non-methane total hydrocarbons emitted by the exhaust tube from the radiator mixing room and radiator fixed spraying room 1 and radiator fixed spraying room 2 after treatment facilities is 3.99mg/m3, benzene undetected, toluene and xylene combined maximum concentration 1.89mg/m3. All of them have reached the maximum allowable emission concentration of surface coating industry in Hebei Province local standard of Industrial Enterprise VOC Emission Control Standard (DB13/2322-2016): the highest concentration of particulate matter emission is 1.962mg/m3, the maximum emission rate is 0.1060kg/h, and they all meet the second class standard in Table 2 of Comprehensive Air Pollutant Emission Standard (GB16297- 1996).
Monitoring the maximum concentration of non-methane total hydrocarbons emitted from the exhaust pipe after monitoring the radiator shower top paint, radiator repaint room 1 and radiator primer drying chamber is 8.91mg/m3, benzene undetected, toluene and xylene combined maximum concentration is 1.76mg/m3. All of them have reached the maximum allowable emission concentration of surface coating industry in Hebei Province Local Standard of VOC Emission Control Standard for Industrial Enterprises (DB 13/2322-2016). The maximum concentration of particulate matter emission is 1.258mg/m3, and the maximum emission rate is 0.1115kg/h. They all meet the second class standard in Table 2 of Comprehensive Air Pollutant Emission Standard (GB16297-1996).
During the monitoring period, the highest concentration of total non-methane hydrocarbons emitted from the exhaust pipe after the treatment facility of the radiator primer and radiator repaint room 2 was 3.17mg/m3.the highest concentration of benzene was not detected, and the total concentration of toluene and xylene was 0.88mg/m3. All of them have reached the maximum allowable emission concentration of surface coating industry in the local standard of Hebei Province, Industrial Enterprise VOC Emission Control Standard (DB 13/2322-2016). The maximum concentration of particulate matter emission is 1.650mg/m3, and the maximum emission rate is 0.1466kg/h. They all meet the second class standard in Table 2 of Comprehensive Air Pollutant Emission Standard (GB16297- 1996).
During the monitoring period, the highest concentration of non-methane total hydrocarbons emitted from the exhaust tube after the radiator was filled with lacquer chamber of 5.01mg/m3, benzene was not detected, and the combined maximum concentration of toluene and xylene was 2.46mg/m3, which reached the local level of Hebei Province. The maximum allowable emission concentration of surface coating industry was stipulated in the Standard of Emission Control Standard of Volatile Organic Compounds for Industrial Enterprises (DB 13/ 2322-2016).
During the monitoring period, the maximum dependence of non-methane total hydrocarbons emitted from the exhaust pipe of the cooler spray-drying integrated chamber 1 treatment facility is 4.76mg/m3,. The highest concentration of undetected benzene and the total concentration of toluene and xylene is 1.71mg/m3, which all meet the maximum allowable emission concentration of surface coating industry in Hebei Province Local Standard of Industrial Enterprise Volatile Organic Compounds Emission Control Standard (DB 13B 2322-2016). The highest concentration of particulate matter emission is 2.159mg/m3, and the maximum emission rate is 0.1099kg/h. All of them have reached the second-class standard in Table 2 of the Comprehensive Emission Standard of Air pollutants (GB16297-1996).
The maximum concentration of non-methane total hydrocarbon emitted from the exhaust tube after the cooler spray-drying integrated chamber 2 treatment facility is 4.01mg/m3, the benzene is not detected, and the combined maximum concentration of toluene and xylene is 1.54mg/m3, which all meet the maximum allowable emission concentration of surface coating industry in Hebei Province local standard of Industrial Enterprise VOC Emission Control Standard (DB 13/2322-2016): the highest concentration of particulate matter emission is 1.876mg/m3. The maximum emission rate is 0.0941kg/h, which meets the second class standard in Table 2 of the Comprehensive Air Pollutant Emission Standard (GB16297- 1996).
During the monitoring period, the highest concentration of non-methane total hydrocarbons emitted from the exhaust pipe after the butterfly valve spray painting (primer, topcoat) room and drying room 1 and drying chamber 2 treatment facilities is 4.01mg/m3, benzene undetected, toluene and xylene combined maximum concentration is 1.41mg/m3, and the lowest removal efficiency of non-methane total hydrocarbons is 71.2%. All meet the maximum allowable emission concentration and related requirements of the surface coating industry (50% of the emission limit) in Table 1 of the Industrial Enterprise VOC Emission Control Standard (DB 13max 2322-2016). The maximum concentration of particulate matter emission is 1.301mg/m3 and the maximum emission rate is 0.0051kg/h. All meet the secondary standards and related requirements in Table 2 of the Comprehensive Emission Standard for Atmospheric Travelling Pollutants (GB16297-1996) (the emission rate is implemented strictly according to 50%).
During the monitoring period, the highest concentration of non-methane total hydrocarbons emitted from the exhaust tube of the activated carbon desorption chamber was 13.54mg/m3, benzene was not detected, toluene and xylene were not detected. All of them meet the emission concentration requirements of other industries in Table 1 of Hebei Provincial Local Standard "Industrial Enterprise VOC Emission Control Standard (DB 13/2322-2016): the highest concentration of particulate matter emission is 0.654mg/m3, and the maximum emission rate is 0.0016kg/h. All of them meet the second class standard of Table 2 of Comprehensive Air Pollutant Emission Standard (GB16297-1996).
During the monitoring period, the highest concentration of unorganized non-methane hydrocarbons emitted from the radiator spraying workshop was 0.98mg/m3, benzene, toluene and xylene were not detected, which met the concentration limits of air pollutants in the workshop in Table 3 of the Control Standard for Volatile Organic Compounds in Industrial Enterprises (DB 13/2322-2016). The maximum concentration of unorganized particulate matter was 0.198mg/m3. Emissions meet the Air Pollutant Comprehensive Emission Standard (GB16297-1996) Table 2 unorganized emission monitoring concentration limit: cooler spraying workshop spray drying outdoor 1m unorganized emission of unorganized methane total concentration of 0.55mg/m3, benzene, toluene, xylene are not detected, which meets the limits of air pollutant concentration at the boundary of production equipment in Table 3 of the Control Standard for Volatile Organic Compounds in Industrial Enterprises (DB 13max 2322-2016): the maximum concentration of unorganized particulate matter is 0.226mg/m3. Emissions meet the Air Pollutant Comprehensive Emission Standard (GB16297-1996) Table 2 unorganized emission monitoring concentration limits: the highest concentration of unorganized unorganized methane hydrocarbons emitted outside the butterfly valve spraying workshop, spray room and drying room is 0.65mg/m3, benzene, toluene and xylene. The emission meets the air pollutant concentration limit of the production workshop in Table 3 of the Industrial Enterprise Volatile Organic Compounds Emission Control Standard (DB 13/ 2322-2016): the maximum concentration of unorganized particulate matter is 0.385mg/m3, and the emission meets the unorganized emission monitoring concentration limit of Table 2 of the Comprehensive Air Pollutant Emission Standard (GB16297-1996):
The highest concentration of total non-methane hydrocarbons at the enterprise boundary is 1.24mg/m3. Benzene, toluene and xylene are not detected, and the emissions meet the concentration limits of air pollutants at the enterprise boundary in Table 2 of the Industrial Enterprise VOCs Emission Control Standard (DB 13/ 2322-2016). The highest concentration of particulates is 0.198mg/m3, which meets the unorganized emission monitoring concentration limit of Table 2 of the Comprehensive Air Pollutant Emission Standard (GB16297-1996).
The highest concentration of total non-methane hydrocarbons in Huafeng living area is 1.20mg/m3, which meets the secondary standard of Ambient Air Quality Non-methane Total Hydrocarbons Limit (DB 13 / 1577-2012): benzene, toluene and xylene are not detected, which meets Industrial Enterprise Design Hygiene Standard (TJ36-79), the highest concentration of particulate matter is 0.166mg/m3, meet Ambient Air Quality Standard (GB3095-2012).
3.Factory boundary noise
During the monitoring period, the daytime noise values of factory boundary noise ranged from 58.4dB (A) -63.9dB (A), which reached the standards of Class 3 in Table 1 of the Environmental Noise Emission Standard for Industrial Enterprises (GB12348-2008). The daytime noise values of the living areas of Huafeng Group were between 50.4 (A) -52.9dB (A), which reached the standards of Class 2 in Table 1 of Acoustic Environmental Quality Standard (GB3096-2008).
4.Solid waste
After domestic waste collection, it is regularly sent to the designated place of the sanitation department for disposal. The waste activated carbon is stored as dangerous waste, desorbed in the plant and then returned to production. According to the desorption of the waste activated carbon in each process, it is replaced once a year, and then desorbed and transported as general waste to the designated place of the sanitation department for disposal. Waste paint buckets of water-based paint are regularly recycled by manufacturers. The paint residue, waste filter cotton, oily paint waste bucket, sewage treatment equipment sludge, internal cleaning residue and hazardous waste from phosphating process produced by the project are classified and temporarily stored in the hazardous waste room of the plant and regularly disposed of by Cangzhou Jihuan Veolia Environmental Service Co., Ltd.
5.Total amount of pollutant discharge
After the EIA approval, the reconstruction project is completed. The annual control index of the total amount of pollutants in the plant is as follows: SO2: 19.200t,NO3: 3.020t,
According to the pollutant discharge situation during the testing period, the total pollutant discharge of the project was calculated as follows: particulate matter: 0.485t/a, non-methane total hydrocarbon: 2.363t/a, xylene: 0.683t : 0.0029t/a: COD : 0.089t/a, NH3-N: 0.003t/a, TN: 0.009t,TP0.0008t/a, total Zinc: 0.0029t/a.
According to the pollutant concentration of the main outlet of the sewage station of Huafeng Industrial Group Company during the monitoring period and the annual discharge of the whole plant, the total discharge amount of wastewater pollutants of the whole plant is calculated as follows: COD: 5.493t/a, total ammonia: 0.579t/a, ammonia nitrogen: 0.215t/a, total zinc: 0.082t/a, total phosphorus: 0.049t/a. Because only this project produces organic waste gas in the whole plant, the organic waste gas emission of the solid project is the organic pollutant emission of the whole plant, the annual non-methane hydrocarbon emission of the whole plant is 2.363t/a, the annual xylene emission is 0.683t/a, the project has no fuel and gas facilities, the SO2 emission is 0t/a, the NO3 emission 0t/a, to sum up, the total pollutant emission of the whole plant meets the total control target.
V. The influence of engineering construction on the environment
During the acceptance monitoring period, the highest concentration of non-methane total hydrocarbons in Huafeng living area was 1. 20mg/m3, which met the secondary standard of Limit of Non-methane Total Hydrocarbons in Ambient Air Quality (DB 13 / 1577-2012): benzene, toluene and xylene were not detected, which met the Hygienic Standard for Industrial Enterprise Design (TJ36-79), and the highest concentration of particulate matter was 0.166mg/m3, which met the Environmental Air Quality Standard (GB3095-2012). The daytime noise value of the living area of Huafeng Group is 50. 4(A) ~52.9dB(A), which met the category 2 standards in Table 1 of Acoustic Environment Quality Standard (GB3096- 2008).
VI.Acceptance conclusion
After on-site inspection, data inspection and report review, the acceptance team put forward the following rectification suggestions:
In strict accordance with the requirements of Construction Project Environmental Impact Assessment Document Examination and Approval and Construction Units Independently Carry Out Environmental Protection Facilities Acceptance Work Guidelines (Trial), Construction Project Completion Environmental Protection Acceptance Technical Guide Pollution Impact Category, improve the acceptance monitoring report.
The inner cavity paint process of the radiator spraying workshop increases the height of the paint recovery tank to prevent paint overflow:
Improve the identification of hazardous waste room and the management of hazardous waste.
Provide feasibility analysis documents for waste gas collection and treatment.
At present, rectification and reform have been completed as required. The project has also implemented various environmental protection systems in accordance with the requirements of environmental assessment and approval, and the discharge standards of waste water, waste gas and noise are up to standard. All solid wastes are disposed of properly, and the acceptance team considers that the project does not belong to the situation of unqualified acceptance and agrees that the project has passed the acceptance of environmental protection after completion.
Head of the acceptance team:
Member of the acceptance team: Wang Shan
Tag:
Related download
Related News
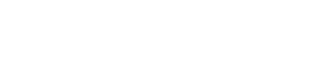
The company is committed to the development of transmission and distribution and control equipment, special equipment, heat exchange equipment, structural metal products manufacturing, as well as metal surface treatment and other manufacturing industries. The subsidiary company, which is dedicated to the production of transformer supporting products: chip radiator, cooler, fan butterfly valve and so on, is one of the important production bases of transformer components in the country.
Contact Us:
Email:hfjlb@163.com
Add: No. 1 Huafeng Road, Songlindian Town, Zhuozhou, Baoding, Hebei province
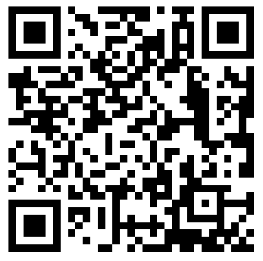
Mobile terminal
All rights reserved ©Hebei Huafeng Industrial Group Co., Ltd. www.300.cn | SEO | City sub-station